A former apprentice at Arey’s Pond Boat Yard and a graduate of The Landing School, Brian Porter is a member of the team that built the AC75 that the American Magic Sailing Team will be using to bring the America’s Cup back home.
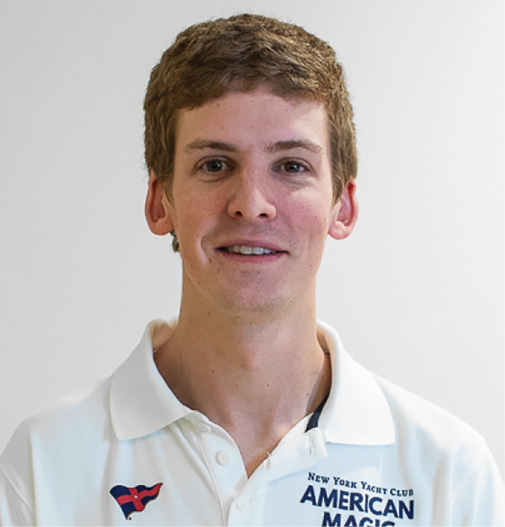
Brian Porter © Amory Ross/American Magic
WindCheck: Where did you grow up, and how old were you when you started sailing?
Brian Porter: I grew up in Orleans, Massachusetts on Cape Cod and still call it my home. I was about 18 or 19 when I first stepped on a sailboat to go sailing. I hadn’t grown up sailing; I considered myself more of a powerboat person although I really enjoyed working on sailboats. The first time I ever went sailing was when I had finished a new build for a customer. I was working as an apprentice at Arey’s Pond Boat Yard in South Orleans at the time, building custom catboats. My boss thought it was a good idea to get me out for a sail so I could learn more about how everything worked. We took the new boat out for a shakedown sail and I remember to this day how cool it felt to be moving along under wind power without the sound of an engine for the first time.
WC: What inspired you to pursue boatbuilding as a career?
BP: I can’t really say any one thing in particular inspired me to become a boatbuilder – I fell in love with the building process. I loved building things from a very young age and I have my father to thank for that. He is a very skilled woodworker and he taught me everything he knew, including having an extreme attention to detail. I took that woodworking knowledge and just applied it to boatbuilding.
While working at Arey’s Pond Boat Yard I said to myself, “This is awesome. I get to build these beautiful boats and I’m getting paid for it.” That’s when I decided to make a career out of it. One of the employees at Arey’s Pond Boat Yard suggested going to a boatbuilding school to really learn the trade, so I enrolled at The Landing School in Arundel, Maine.
In my first year at The Landing School, we built a 30-foot cold molded performance sailboat where I learned about different boatbuilding methods. Learning all the materials and different ways to use them was all part of what I enjoyed. I learned everything about building a boat from start to finish, like setting up building jigs, to planking the boat, fiberglassing, fairing and painting, running wire, and installing the diesel engine and the supporting systems. Seeing a boat take its shape is something I find very rewarding, and it’s all helped me become a well-rounded boatbuilder for American Magic.
WC: Did you have any significant mentors in the boatbuilding trade? If so, what are the most important things you learned from them?
BP: My most significant mentors are the bosses and co-workers I’ve worked with over the years. Everyone brings their own methods and styles to the shop. You pick up great tricks and techniques from people you work with. I have to give a few people credit at the beginning of my career like Suzanne Leahy, Danny Gould, and Rick Barkhuff. They always took the time to teach me something. They showed me that no matter what the task is, no matter how difficult, or whether you know how to build it or not, there is always a way to get it done – you just have to start somewhere. Of course, I have to give my current bosses credit also for bringing my boatbuilding to the next level…you just learn so much during a Cup campaign!
WC: What are your responsibilities as a member of the Production Team?
BP: My responsibilities vary from day to day depending on where we are along the build process. If we are just starting a new part, I will often be involved with constructing the building jig, like the deck jig, for example. It’s very similar to cold molding. This is an important step in that everything must be accurate and correct, or the part may not fit the boat or create complications down the line. I will then help laminate the deck and hull, which takes months to do. On boat two, I was cutting the pre-preg carbon for everyone laminating in the hull. It comes on rolls and I would get measurements, record them, and go cut a bunch of lengths and give it to the person working in that area, while trying to waste as little as possible. I had quite the task trying to keep carbon fed to everyone quick enough so that nobody was waiting on me.
During the hull fit-out, which is my favorite part of the build, I will be given a part like a frame or stringer for example, that has to go in exactly the correct position on the boat. I’ll start by laying out where the part goes inside the boat and then I’ll cut and fit the part to the layout, making sure it fits with very tight tolerances to reduce excess glue filling unnecessary gaps for weight reduction. Once its fit I’ll prep it for glue, weigh it, make jigs to hold the part perfectly in place while the glue hardens, and then glue it in. Once it’s glued in, I’ll generally move onto fitting the next part that needs to go in, or prep it for laminating and laminate it. My main responsibility is to carry out all my tasks as accurately as possible.
WC: Please describe “a typical day” in the American Magic boat shop.
BP: My day starts with a full shop meeting first thing in the morning. The build manager will go over a job list and who’s doing what and what has to get completed by the end of that day and week. I will gather my tools for my job and set myself up with a vacuum and airlines or whatever it might be for the day, and start my task. If I’m not fitting parts, I could be working on a mold for a new part or getting ready to laminate a part into the boat. All parts get laminated into the boat after they have been glued in. We get drawings of the part with dimensions of where it belongs and what the laminate needs to be for taping the part in, so I’ll measure and lay out the taping details on the boat and prep the surface with sandpaper.
Immaculate surface prep is crucial for a strong bond. I’ll take measurements of what I have prepped for vacuum bagging supply and what I need for carbon to do the job. We have a small, closed-off room with all our vacuum bagging and carbon consumables where we cut and prep what we need. I’ll prep a wet-out table for wetting the carbon out with epoxy. We have a very strict “recipe” to follow to ensure all secondary bonding is carried out in an accurate, uniform fashion. I will follow that recipe through the entire lamination. Each laminate, no matter how big or small, is very important and will take a few hours to complete from start to finish. After I finish a laminate, I will either start prepping for another laminate or look at the drawings for the next task and start that. There is never any downtime between jobs – you finish one and jump into the next. If it’s late in the day, everyone checks in with other people to see if they need a hand finishing up their project for the day.
WC: How is the new boat, Patriot, coming along?
BP: Patriot is coming along great. We have had our challenges along the way like you always have with every build, but having COVID-19 impact everything certainly gave us some different challenges to get through.
WC: What’s the best part of your job?
BP: The best part of my job is seeing the finished product out on the water sailing. Considering how much hard work, effort, and technology goes into it, seeing it all come together at the end is very rewarding. It might be hard to enjoy it during the time of the construction but to see people’s reaction and seeing the boat on the Internet is pretty cool. The best days are when the sailing team has a successful day on the water.
WC: Please tell us about he sailing that you enjoy.
BP: The sailing that I enjoy the most is bumping around Pleasant Bay in a catboat in the afternoon, with a beer in hand. Pleasant Bay is filled with shallow channels that weave through sandbars, marshes and small islands that can really only be navigated on a sunny day with a shallow draft boat. It makes for a fun time.
WC: What’s your advice for young sailors aspiring to have a job like yours?
BP: Be a sponge. Absorb as much information as you can. If you want to learn boatbuilding, go to a good boatbuilding school. You will need a great work ethic and work very hard for it. Make good connections with people. You never know where a simple acquaintance might take you.
WC: Thank you very much Brian. We suspect you’ll soon be adding “America’s Cup-winning boatbuilder” to your resumé!
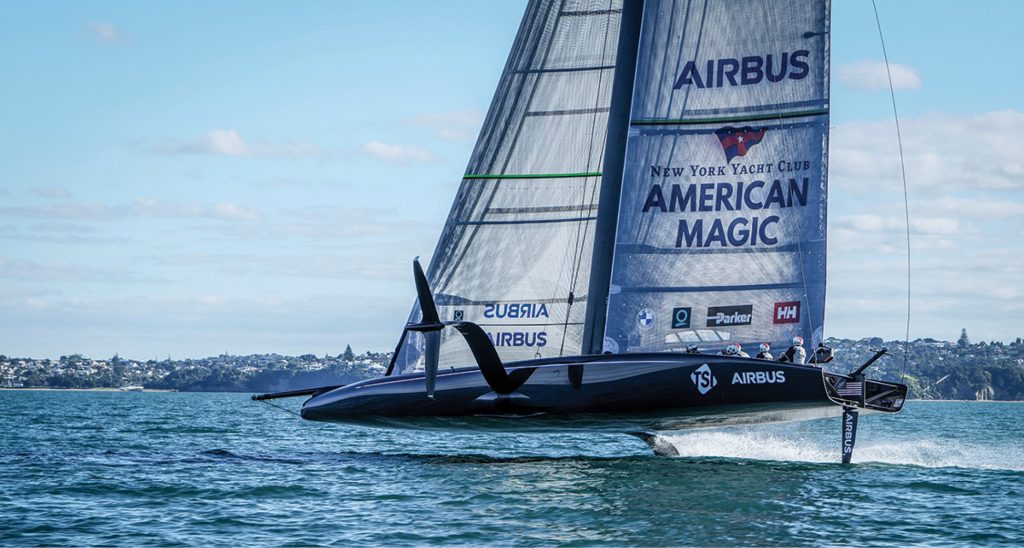
Defiant’s first sail in Auckland © Ryan Pellett/American Magic
Special thanks to New York Yacht Club American Magic Communications Director Will Ricketson for facilitating this interview. ■