Story and photos by Roger Hughes
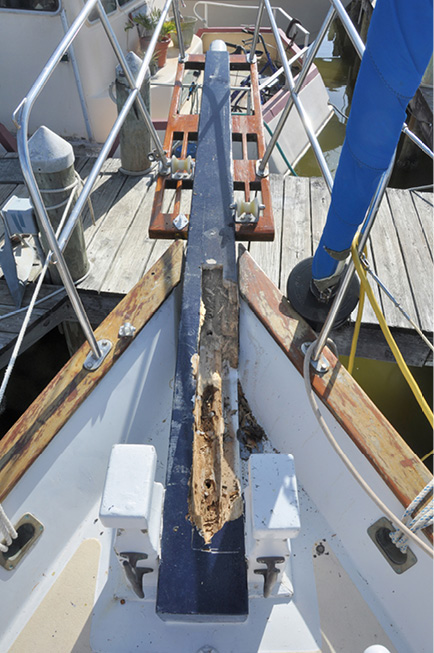
Rotten bowsprit
The first indication there was a problem with the bowsprit on my 1977 Down East 45 schooner was when I was hoisted up the foremast using the electric windlass which was bolted on top of the bowsprit. The operator mentioned the windlass “moved” as he hoisted me using the winding drum.
When I came down the mast I saw what he was talking about, because the windlass was noticeably out of square on the bowsprit. Clearly something was amiss, although I couldn’t see anything wrong with the painted wooden bowsprit. I checked the four long threaded rods securing the windlass through the foredeck in the chain locker, and they were all nicely tight.
On deck again, it didn’t take five minutes probing with a screwdriver to realize there was some seriously rotten wood beneath the windlass. Before long I had the windlass removed, which brought more soft wood out with the four threaded rods. Further scouring with a chisel revealed extensive rot in the nearly ten-foot bowsprit.
At first I hoped it would be possible to repair the ‘sprit in-situ, by scarfing some new planks in to replace the damaged ones. But that was ruled out as I scoured more and more soft wood from the interior of the spar. I gave up after a length of 38 inches! Clearly the boat needed a completely new bowsprit.
Britannia’s bowsprit was a tapered lamination of nine sections of timber glued together. It measured nine feet, six inches long, eight inches square at the heel and five inches square at the crance iron. The previous owner’s log showed it had been installed in February 2005, which didn’t persuade me much towards a third bowsprit in wood. But if I was to make it in anything else, it had to be at least as strong as the previous one.
When considering bowsprit strength there are a number of factors to take into account. When under sail there is an upwards pull on the ‘sprit which varies depending on the point of sailing, the wind strength and of course the size of the headsail(s). This upward pressure is resisted by a number of things, mainly the bobstay, (and in Britannia’s case also a dolphin striker which transmits some load into the bow), the bowsprit shrouds, and the actual strength of the ‘sprit itself, and how it is secured to the deck. If all fittings are correctly tensioned the opposing forces result in a mainly compression force on the bowsprit, pushing it backwards.
These interactions would be fairly easy to calculate in a simple static force diagram. However, a sailboat is hardly static and a major unknown factor is when the bow ‘scends’ into a head sea, plunging the complete pulpit into solid water. This imposes goodness knows what loads on the structure, and nobody –including a sailboat architect – could tell me what these extra loads might be.
A friend loaned me Skene’s Elements of Yacht Design. This had a small section on bobstays but surprisingly nothing about bowsprits, though it does include the sentence, “Since impact loads like head seas cannot be determined accurately, most designers apply a factor of three to five in their estimates.” That struck me as a pretty wide margin of error, and it seemed in the final analysis, it was all based on experience and perhaps destruction tests, none of which was helpful to me.
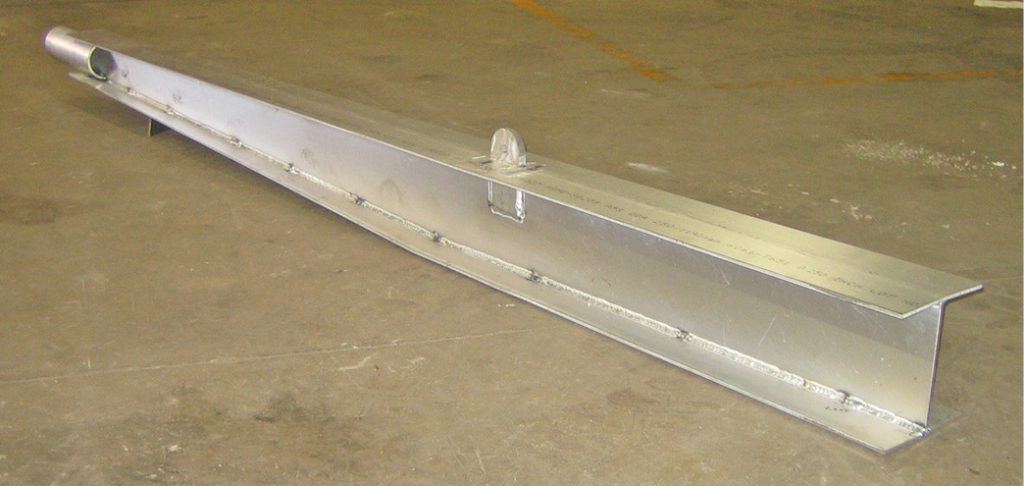
Aluminum bowsprit construction
Alternatives and estimates
I did a drawing of the bowsprit and sent it to three wooden boat builders, who all said they could “easily” make one in Douglas Fir. However, on seeing “the complexity of the job” one declined to quote and then came the next shocks! One price was $2,875 and the other $3,278! Apparently, the wood had to be shipped from the Pacific Northwest—about as far as it could be from where Britannia was moored in Florida. Also, no actual time for completion was given by either builder, even though I specifically asked for it so I could plan the operation. It was obvious none of these people really wanted the job.
My next possible option was to see if I could buy the wood somewhere and build it myself. I located a lumber supplier in Minnesota, who quoted $830 for four 2-inch thick finished straight grained planks of Douglas Fir, 10 feet long and 8 inches wide. Last time I looked at an atlas, Minnesota was not in the Pacific Northwest.
Building the ‘sprit myself would be the cheapest way, but a daunting task. First, gluing and clamping the planks together, then shaping the massive billet—over 200 lbs and about as big as a railroad tie—into a taper, with a 4-inch perfectly round section on the end to carry the crance iron. Additionally, all this would have to be done with hand tools, outside on the dock and subject to the weather, because I had no covered facility.
Over the years I have done some major projects on Britannia, including changing the rig from a ketch to a schooner, but this bowsprit was just too much for me at that time. I decided to explore the possibility of having the thing fabricated in aluminum. At least it couldn’t go rotten and would likely be lighter.
Luckily, my son-in-law Jim is a qualified patent engineer and he offered advice on an aluminum design. After researching different types of aluminum, I decided to specify ¼-inch thick 6061 structural aluminum plate. This is as hard as nails and much stronger than regular aluminum. Drilling it is like drilling stainless steel.
The new ‘sprit needed to be the same shape and size as the existing spar so everything would bolt back in the same place. I therefore designed a box section with a vertical central spine all the way along the inside. This formed an ‘I’ beam, which is well known for stiffness in both bending and compression.
Two aluminum fabricating companies gave me estimates. One was $1,525, including powder coating both the bowsprit and crance iron. The other was $2,200 in raw unpainted aluminum. It won’t be difficult for boat owners to guess which was the ‘marine’ fabricator’s quote, as opposed to a regular welding company.
I was also interested in comparing the weight of an aluminum structure against a wooden one. I guessed the existing spar was made of something like Douglas Fir, which weighs roughly 35 lbs per cubic foot. I calculated the whole bowsprit was 3.24 cu ft., which made it about 113 lbs. The weight of ¼- inch 6061 aluminum sheet is 3.56 lbs per square foot. I worked out the square footage of each piece in the assembly, which all added up to 27.10 sq ft. This, including a round tube at the tip to carry the crance iron, gave a weight of about 100 lbs.
I therefore decided to have the bowsprit made in aluminum, and gave the job to a welding firm in St. Cloud, near Orlando. They had done work for me before and I knew the excellent quality of their welding. Another advantage was that they could start the job almost immediately.
Construction
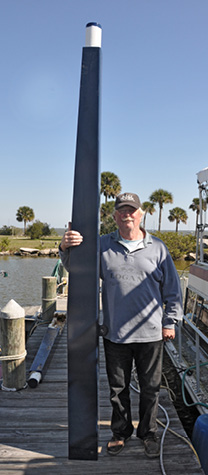
The author displays the new ‘sprit.
After all the pieces had been sheared out of a 10-foot x 4-foot sheet, the top and bottom sections were welded to the center spine. The bottom was bent slightly to form the underneath taper towards the tip. A new staysail bracket was also welded through a slot in the top plate. The original bracket was bolted through the deck, so my design avoided two more potential leaks. A 4-inch diameter tube was welded on the tip to carry the crance iron.
The two sides were then welded to the top and bottom to complete the box. This resulted in a very stiff spar which looked magnificent in its new dark blue livery, matching the rest of the spars and topside stripe. It arrived exactly two weeks from placing the order and weighed 96 lbs—I was 4 lbs out in my calculation!
I asked for the heel plate to be screwed on the end of the bowsprit, so I could bolt it to the two samson posts (bitts) from inside. I also drilled two holes in the bottom, to drain any water which might find its way into the interior.
The damaged bowsprit was still in place and in order to remove it I supported the pulpit and grating with halyards from the foremast, which saved unbolting those cumbersome items from each other. Next, I unbolted all the fasteners holding the grating to the bowsprit and deck. Then with a few willing helpers the damaged bowsprit was levered clear from the bow. The old ‘sprit weighed 116 lbs, so allowing for the missing rotten wood I was 3 lbs out with that calculation. I filled all the holes in the deck, then primed and repainted the area.
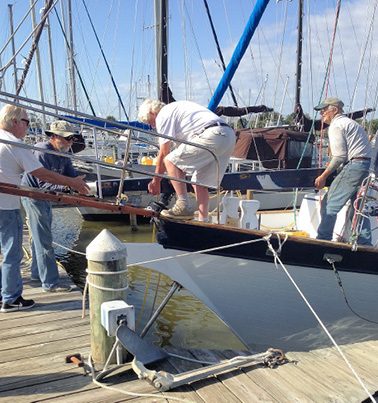
Removing the old bowsprit
Reassembly
When everything was ready, the new bowsprit was pushed in place and carefully lined up with the gratings and samson posts. The long threaded rods to hold the Maxwell windlass pass straight through the bowsprit into the chain locker and help secure the ‘sprit to the deck. Holes were then piloted though the samson posts and the ‘sprit bolted to the posts from inside the tube. Holes were then piloted through the bowsprit and the gratings bolted in place, using the original stainless threaded rods.
The two large bronze anchor rollers never revolved properly since I had the boat, and the chain and anchor grated against them. Before fitting them back I reamed the ½-inch holes clean then drilled and tapped an oil hole into the center of each roller. Oil could then be poured in periodically to keep the rollers smooth running. I screwed a grub screw into the holes to keep water out.
I had sanded the two gratings, and three coats of varnish restored them like new. I had to make fourteen 1-inch, and six ¼-inch teak plugs to cover the holes in the gratings and samson posts. All made by hand, because I didn’t have plug cutters for those sizes. All joins in the ‘sprit and deck were caulked liberally with 3M 5000. The crance iron, which had been powder coated white, was then pushed on its tube and the jib stay, forestay, bobstay and shrouds relocated and tensioned.
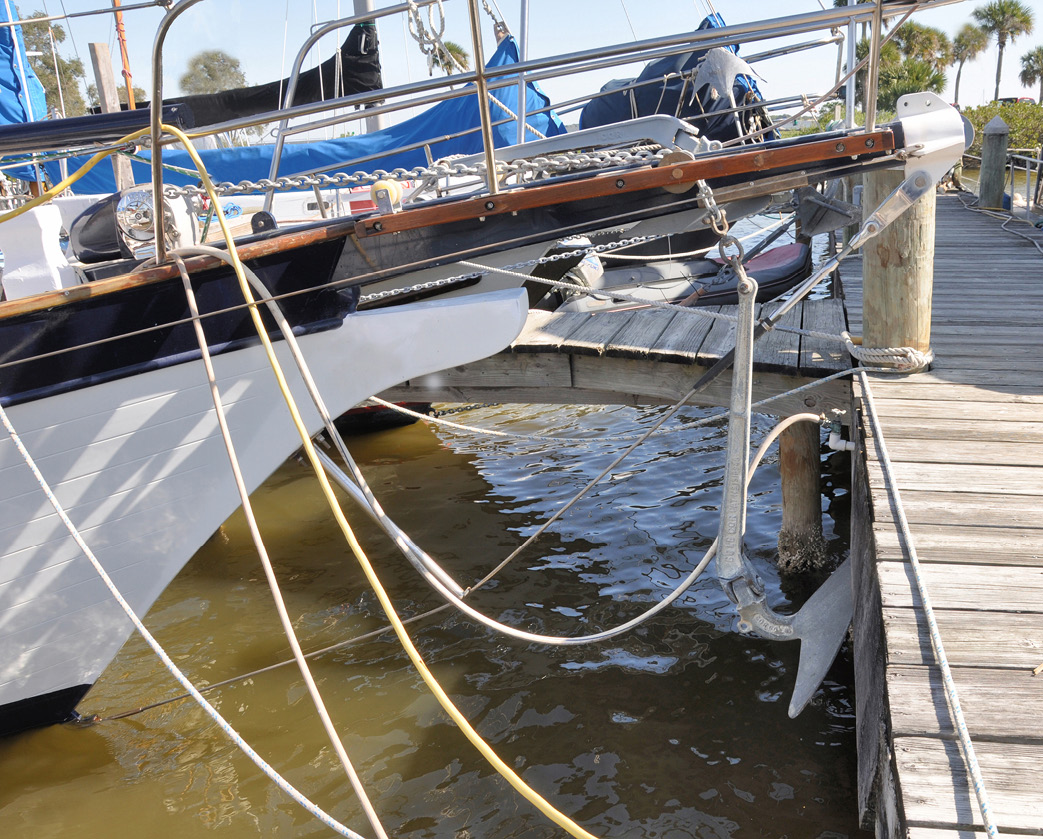
Testing the new ‘sprit
All this heaving and maneuvering was done with the boat in the water and the bow sticking over the dock. This was easier and cheaper than hauling her, because we didn’t need scaffolding or ladders as we would need on the hard, and we could also continue to live aboard. The reassembly took three days, during which the ‘sprit was removed and replaced for adjustments seven times.
Finally, I wondered how we might test the strength and rigidity of the new structure. Of course, the ultimate test would be at sea in heavy weather, but I also decided to conduct a simple static test by bowsing down the bowsprit, to see what happened.
I disconnected the jib and staysail stays, then with only the bobstay and shrouds attached I hooked the anchor under the dock, directly below the bowsprit. Then I tensioned the chain with the windlass, which I was pleased to see never even budged. This pulled the bow downwards and the bobstay bracket disappeared underwater. A second touch on the winch button pulled the bow down further, and the chain was now bar tight. Amazingly, the bobstay also remained taught – it would’ve gone slack if there had been any deflection between the ‘sprit and the bow.
At this point I heard ominous creaking from the dock timbers, so I quickly slacked it off. Hauling a heavy displacement boat down like this imposed some impressive loads on the bowsprit, but there was absolutely no evidence of shifting, or paint cracking, anywhere along the new bowsprit.
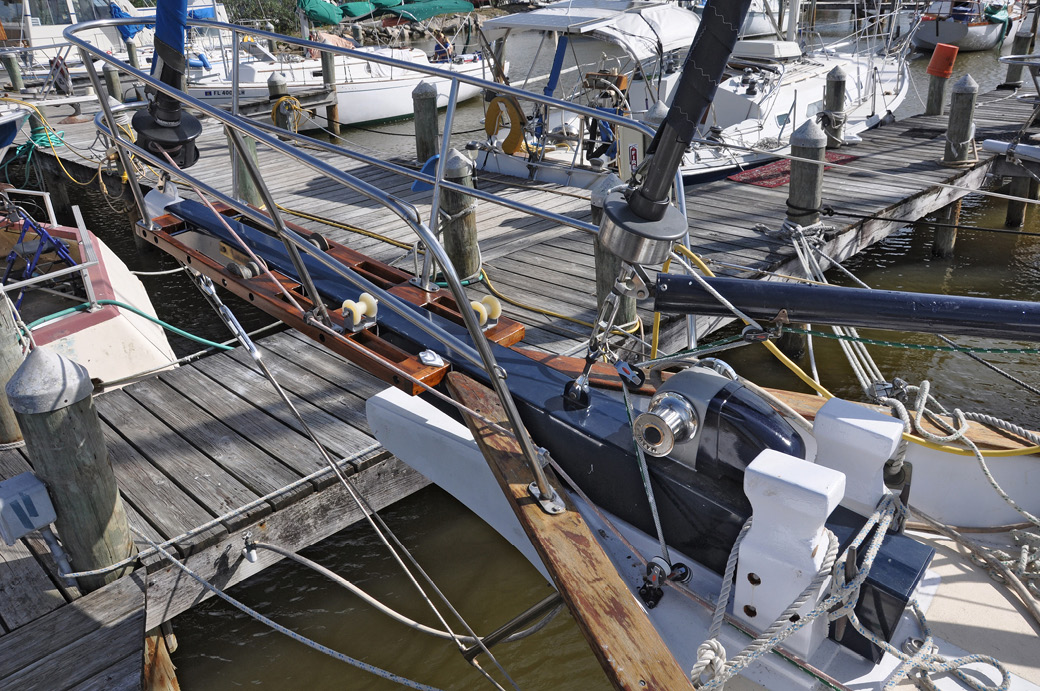
Installation complete
On seeing the finished result Jim wrote, “Based on the back-of-the-envelope calculations I did, and the way it’s been built, I think your new bowsprit is anywhere from five to ten times stiffer than a wooden job, and can probably withstand a load at least five times greater before yield or fracture.” This was good to hear, but I hope old Neptune doesn’t have other ideas. ■
A freelance writer for boating magazines in the US, UK, Australia and New Zealand, Roger Hughes is an Englishman who lives near New Bern, NC, and has been messing about on boats for half a century as a professional captain, charterer, restorer, sailing instructor and happy imbiber – on a lot of boats. He recently completed a restoration and extensive modification of a once run-down 50-foot ketch, renamed Britannia. This included converting the rig into a brigantine schooner, with a rollaway squaresail on the foremast, along with many more innovations and inventions, like a full size hot-tub bath and electric dinghy hoist.
All of Roger’s published articles can be read free of charge at schooner-britannia.com. People are free to copy any of the ideas, and Roger also offers extended advice, on a consulting basis, to anyone wishing further information or help.